Nineteen thousand kilometers, 200 cities and more than 150 artisans across 19 states in India. Those were the starting ingredients for Wilson College of Textiles alumnus Adhiraj Shinde and his wife Aishwarya Lahariya when they decided to co-found Jiwya, an entirely plant-based luxury apparel and lifestyle brand.
Heritage art meets plant-based future
Shinde, who earned an M.S. in Textile Engineering from the Wilson College, says the idea for Jiwya came from the couple’s long shared frustration with the unsustainable and polluting practices of modern clothing production.
“We always used to discuss how polluting the textile industry is,” Shinde explains. “It’s one of the top three polluting industries in the world, and now with fast fashion so many people are buying clothes and just throwing them in the landfills.”
Their goal was to turn fast fashion on its head by creating a new kind of clothing company: entirely plant-based, direct-to-consumer, handmade clothing that will last for years to come.
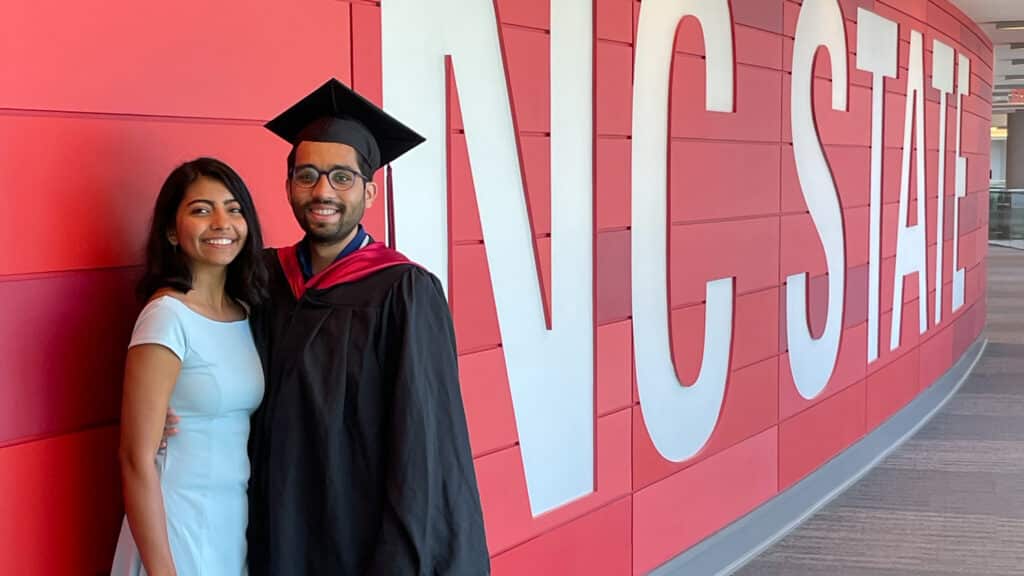
In 2022 the couple moved back to India where they spent a year researching and planning how to build this company using the resources, infrastructure and award-winning artisans around them.
“We drove around 12,000 miles and visited 19 states,” Shinde says. “And we connected with the heritage grassroots artisans of India.”
They learned about each of the artisan’s unique forms of textile art, some of which their families had been perfecting for more than 10 generations. Shinde’s aim was to convince them to create their art using only plant-based materials.
“No plastics, no synthetics, not even the buttons or packaging material,” Shinde explains. “Everything has to be either compostable, or, if not, at least recyclable.”
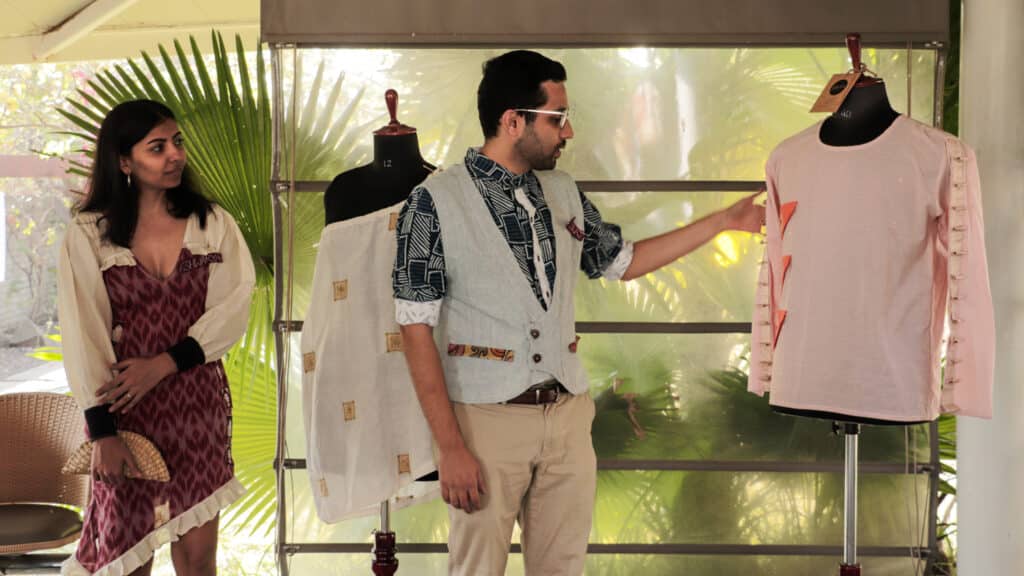
They spent months sourcing materials from local ecosystems, using traceable supply chains so consumers could see exactly where the materials came from. Their goal was to find materials that were raw and unbleached, free of synthetic coatings and solvents, and manufactured using non-polluting methods. They even complete a portion of their fabric processing in-house to ensure the entire process fits their rigorous sustainability standards.
“We had to really scout and look all over the country, get samples, get them tested and go down to the micro level to make sure that there was absolutely no plastic because that’s what we wanted to deliver,” Shinde says.
The fabrics created by the artisans using these non-plastic materials were then sent to the Jiwya manufacturing facility where Lahariya designs their products. The result was a collection of beautiful and one-of-a-kind pieces, each made with fabric featuring at least two forms of Indian textile art made from unbleached, rain-fed cotton.
Building strong foundations
While Jiwya has matured into the fully realized company it is today, the original ideas it grew from were born during Shinde’s time at the college where he worked in Assistant Professor Bryan Ormond’s lab at the Textile Protection and Comfort Center (TPACC).
“One of the main things I was working on at TPACC was working with synthetic chemicals,” Shinde says. “I was astonished at how the firefighters wear these kinds of materials where it’s so toxic, it’s right next to their skin. So it was always in the back of my mind how synthetic chemicals and colors and dyes can be eliminated.”
For Shinde, the skills he learned and experiences he had while studying at the college and working with TPACC built the foundation he needed to create Jiwya.
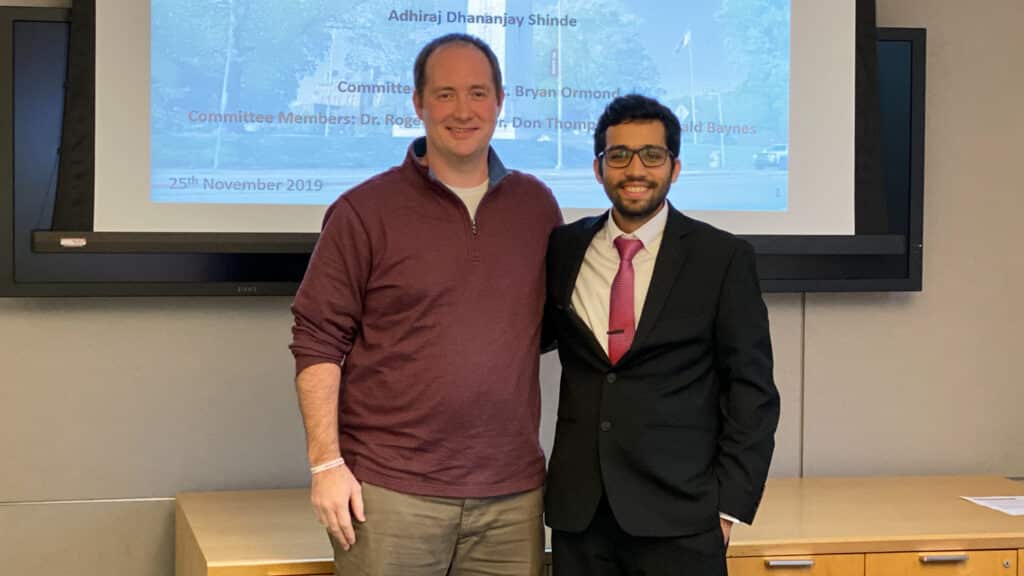
“One of the biggest things we hope students gain is the ability to see a problem and solve it,” Ormond says. “If you run into a wall, if you get a block in front of you or if something doesn’t work right how do you not just shut down and stop, but look for those answers? How do we get around it? How do we resolve it?”
“Being able to think outside the box, being innovative, solving the problem at hand and not doing something that is just fancy or cool to do but solves a problem was always at the forefront and is what we were being pushed to do by mentors and professors at NC State,” Shinde says. “So that was really thought provoking for me.”
Along with a think and do mindset, Shinde also says the technical skills he learned at TPACC gave him the confidence and knowledge he needed when starting Jiwya.
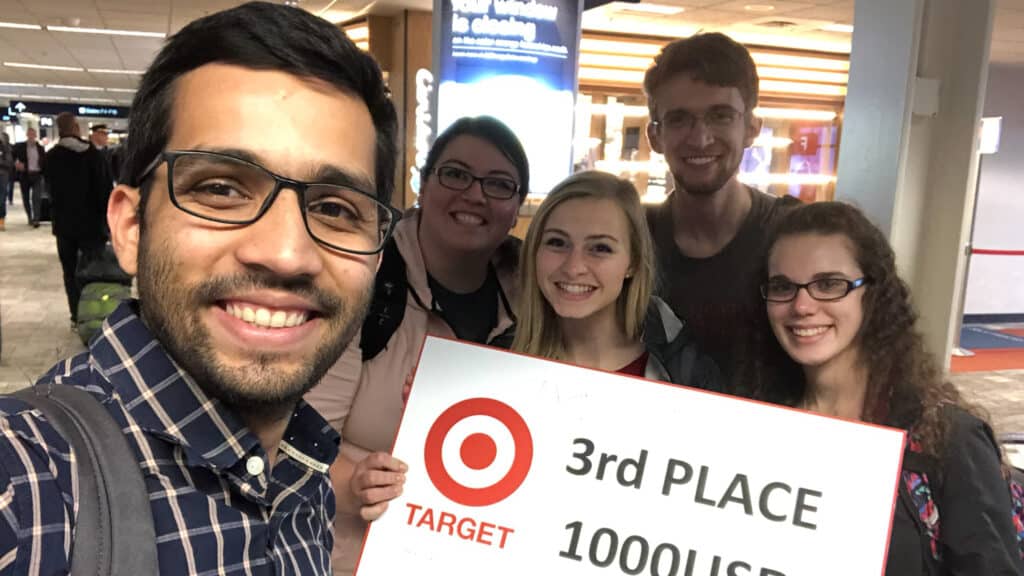
“I had to work with business development, executives and engineers who were really highly technical,” he says. “So that really helped me in my startup where we were using everything natural. So when someone tells me ‘Oh this is natural, this is vegan leather.’ I can immediately question, ‘Well what about that polyurethane coating that you’re putting on it?’”
Looking forward, Shinde hopes to expand Jiwya and bring their vision of clean, earth-friendly clothing to a global audience.
“We want to create big change in the fashion industry,” he says. “Let the fashion industry know that fashionable can be purely plant based.”
This post was originally published in Wilson College of Textiles News.
- Categories: